Why Does Electromagnetic Compatibility (EMC) Need to Be Guaranteed for Some Cables?
Everyone’s familiar with the phenomenon of electromagnetic noise: the WiFi connection suddenly stops working, the radio crackles or the telephone handset is making a noise. The sources of these unwanted signals can be very diverse. They range from mobile phones, laptops and transmitters to transients in power transmission lines to motors and power sources. The so-called cause is interference. It occurs whenever two or more electromagnetic radio waves collide. Interference can be destructive or constructive; the troublesome one is actually the positive-sounding one variant. During destructive interference the waves cancel each other out, but constructive interference causes the waves to overlap and amplify each other.
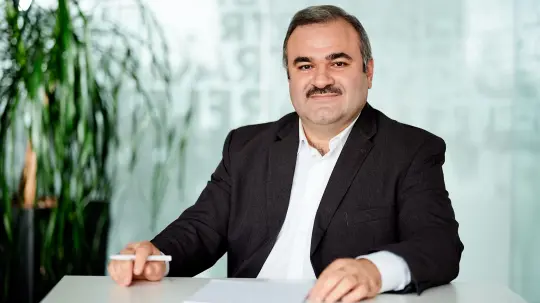
This results in noise, which in extreme cases, may cause devices or entire systems to stop working altogether. To avoid this, products must be made with electro-magnetic compatibility (EMC). The electromagnetic compatibility of cables and wires is achieved through screening. The screen surrounds the electric field and prevents both penetration and emission of electromagnetic waves. EMC requirements for screened cables are regulated by international and national standards. The surface transfer impedance (also called coupling resistance) is a measure of the screening quality and is defined as the voltage ratio on the screening of the disturbed system to the current in the disturbing system. In industrial applications, for example, a screen transfer impedance smaller than 150 MOhm/m at 30 MHz is required. Measurements are based on DIN EN 50289-1-6 and IEC 62153-4-3. The materials used for screening always depend on the application area. In antenna engineering, for example, corrugated copper screens are placed around the coaxial cables. By contrast, the screened cables used in industrial applications must be flexible and withstand particularly high stresses. HELUKABEL has developed a custom screened cable to provide effective screening for a plasma system, even when operated by a 50 kHz high frequency clocked power supply. In this case, a “real screen” comprising of different foils, fleeces and braids was used. A high level of coverage in the braid is important, but the “the more the merrier” principle does not apply here. Using more copper might, for example, worsen the transfer impedance value and hence, the screening effect. The constantly rising demand for hybrid constructions (e.g. those with combined power and data cables) is increasing the importance of effective screening. The cable designer's skill therefore lies in developing innovative screening solutions that take into account the application’s parameters, costs and individual customer requirements in order to ensure high levels of operational reliability and noise immunity.